- :
- Protege5 2003
Here is my fix for the compressor failure problem in fan speeds 2 and 3. The small circuit which is installed separates the control board sense line from the fan speed control line 1, and supplies the former with a reliably low voltage when the blower is running. No modifications of the control board itself are required, although 3 wires in the harness going to it must be cut and spliced. Except for the relay you should be able to get all of the needed components at Radio Shack. In the circuit diagram the thick lines with arrows are the wires that run from the new circuit to the cut wires, and these lines are colored like the respective wires. The solid black circles are solder points. Here is a diagram of the circuit.
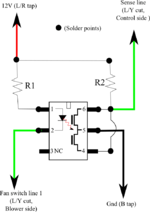
The circuit works in this way. When the fan is off the wire to pin 2 floats to 12V (pulled high by the blower resistor and the blower), so there is no voltage across the LED in the solid state relay. This turns off the two FETs so no current flows through them to ground. The 10000 Ohm resistor R2 pulls the climate control sensor line high (pin 6) and the climate control unit turns off the compressor. If the fan is in postions 1,2,3, or 4 pin 2 will be at 1 to 1.5 volts, so there will be at least 10 volts between pin 2 and +12V. The 1000 Ohm resistor R1 limits the current to about 10mA. That is 5X the rated "on" for the LED, and 1/5th the maximum current. A little power will be dissipated so a 1/2W resistor is used. No significant power is dissipated in R2, so a 1/8W resistor is sufficient. With 10mA flowing through the LED the light emitted (not visible, it is inside the IC) turns on both FETs, which are wired in parallel by the jumper between pins 4 and 6 (the one bent trace). The FETs effectively short pin 6 to ground and pull the sense line to that voltage too. The climate control unit will turn the compressor on. The control unit will reliably turn on the AC because the voltage it sees is not close to its on/off threshold (as in the stock situation) but is roughly 1V
below that threshold, so it will not be confused.
Disclaimer and cautions. You do this at your own risk. If this breaks your car, too bad. You must be extremely careful while soldering inside the car. Unless you have prehensile toes or a third arm you are going to need a helper to hold the iron while you do some of the work. NEVER set the iron down in the car, even in a standard iron stand, because if it falls over it is more than hot enough to destroy any plastic it touches. Touching the seat fabric or carpet could well result in a fire. Let us not even go into the damage a hot iron can do to your person. Always wear eye protection when soldering. Unless you aspire to a case of COPD open all the car windows, or better yet, all the doors, and don't breath the smoke from the soldering. OK, you have been warned.
Parts needed:
Instructions:
1. Open the dual printed circuit board and snap the two halves apart at the dotted line, only one will be used.
2. Open the project enclosure, set aside the metal plate (it will not be used).
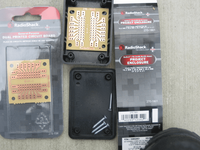
3. Turn the circuit board so that the center of the IC will run up the center of the enclosure. It won't quite fit. Use the flat file to narrow the sides of the board or to remove the vertical ridges on the inside of the enclosure until it will lay flat in the bottom of the enclosure on the four small cylindrical supports there. (Don't breath the dust.) Alternatively, you could trim off the vertical plastic ridges on the enclosure with a razor blade or a chisel.
4. The holes in the circuit board do not quite line up with the holes on the supports.
Extend the holes on one end of the board inward using the small round file. A drill could also be used.
5. Place the components on the nonmetallic part of the circuit board. Bend the leads outward on the metallic side so that they stay in place while being soldered. Note the little white dot in the upper left corner of the IC is pin 1.
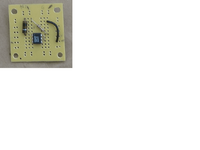
6. Flip the board over and solder the components in place as shown in the pictures. Be sure the iron is fully warmed up before soldering. Do the pins on the IC as quickly as possible - ICs do not like high temperatures. Check for solder bridges and remove any that might have formed. The black wire on the board isn't needed, just solder the long black wire in where the lower end of the black wire is. (I thought I might need to put a resistor in where the short black wire is, but in the end it wasn't needed.) Sorry about the blurry image, here is what the back of the board will look like:
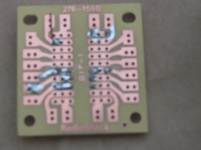
7. Cut 2 18" pieces of the green wire and 1 each 18" pieces of the red and black wire. Strip 1/4" from one end and a bit more from the other. Solder the 1/4" ends into the circuit board as shown in the diagrams and pictures.
8. Trim the excess wire and component leads on the metallic side. This is what the board will look like with the wires in place.
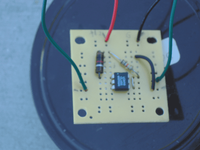
9. Test the circuit. Attach the Red wire to the positive terminal of the 9V battery, and the Black wire to the negative terminal. Set the multimeter to measure in the lowest DC voltage range greater than 9V. For most multimeters that is most likely 20VDC. [Some multimeters apparently have a "9V" setting - that is for testing batteries, not for measuring voltage. Do not use it.] Connect it between the negative terminal of the battery and the green wire attached to pin 6. It should read 9V (whatever the battery is reading.) Touch the Green wire attached to pin 2 of the IC to the negative terminal of the battery. The voltmeter should drop to very close to zero volts.
(continued in next post)
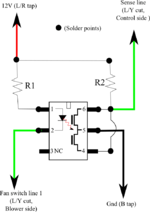
The circuit works in this way. When the fan is off the wire to pin 2 floats to 12V (pulled high by the blower resistor and the blower), so there is no voltage across the LED in the solid state relay. This turns off the two FETs so no current flows through them to ground. The 10000 Ohm resistor R2 pulls the climate control sensor line high (pin 6) and the climate control unit turns off the compressor. If the fan is in postions 1,2,3, or 4 pin 2 will be at 1 to 1.5 volts, so there will be at least 10 volts between pin 2 and +12V. The 1000 Ohm resistor R1 limits the current to about 10mA. That is 5X the rated "on" for the LED, and 1/5th the maximum current. A little power will be dissipated so a 1/2W resistor is used. No significant power is dissipated in R2, so a 1/8W resistor is sufficient. With 10mA flowing through the LED the light emitted (not visible, it is inside the IC) turns on both FETs, which are wired in parallel by the jumper between pins 4 and 6 (the one bent trace). The FETs effectively short pin 6 to ground and pull the sense line to that voltage too. The climate control unit will turn the compressor on. The control unit will reliably turn on the AC because the voltage it sees is not close to its on/off threshold (as in the stock situation) but is roughly 1V
below that threshold, so it will not be confused.
Disclaimer and cautions. You do this at your own risk. If this breaks your car, too bad. You must be extremely careful while soldering inside the car. Unless you have prehensile toes or a third arm you are going to need a helper to hold the iron while you do some of the work. NEVER set the iron down in the car, even in a standard iron stand, because if it falls over it is more than hot enough to destroy any plastic it touches. Touching the seat fabric or carpet could well result in a fire. Let us not even go into the damage a hot iron can do to your person. Always wear eye protection when soldering. Unless you aspire to a case of COPD open all the car windows, or better yet, all the doors, and don't breath the smoke from the soldering. OK, you have been warned.
Parts needed:
Code:
1x Clare LCA110 solid state relay. Digikey part number CLA101-ND $2.49 + shipping.
1x Radio Shack 278-1221, 22 Gauge solid hook up wire, 3 30ft rolls, rated 300V 80C.
1x Radio Shack 276-159, Dual printed circuit board.
1x Radio Shack 270-1801, Project Enclosure, 3" x 2" x 1"
1 foot heat shrink tubing (wide enough to hold 3 wires of the 22 Gauge, I had
some on hand, Radio Shack sells this too.)
1x 1,000 Ohm 1/2 watt resistor. (R1 in the diagram)
1x 10,000 Ohm 1/8 watt resistor. (R2 in the diagram)
2x zip ties (around 8")
Fine or narrow solder, with flux, "no clean". (Note, [COLOR="red"]NOT ACID CORE![/COLOR]!!!)
Tools needed:
Philips head screw driver.
Eye protection (when soldering)
Flat file.
Small round file.
25-40W soldering iron with a small tip (conical or flat).
Something to clean the iron tip: best is a bronze "sponge" or shavings, but a
wad of damp paper towels will also work.
Wire stripper/cutter/screw cutter
Multimeter
Drill and bits
Extension cord
9V battery (optional)
Instructions:
1. Open the dual printed circuit board and snap the two halves apart at the dotted line, only one will be used.
2. Open the project enclosure, set aside the metal plate (it will not be used).
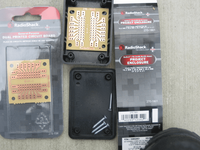
3. Turn the circuit board so that the center of the IC will run up the center of the enclosure. It won't quite fit. Use the flat file to narrow the sides of the board or to remove the vertical ridges on the inside of the enclosure until it will lay flat in the bottom of the enclosure on the four small cylindrical supports there. (Don't breath the dust.) Alternatively, you could trim off the vertical plastic ridges on the enclosure with a razor blade or a chisel.
4. The holes in the circuit board do not quite line up with the holes on the supports.
Extend the holes on one end of the board inward using the small round file. A drill could also be used.
5. Place the components on the nonmetallic part of the circuit board. Bend the leads outward on the metallic side so that they stay in place while being soldered. Note the little white dot in the upper left corner of the IC is pin 1.
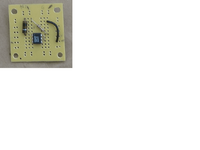
6. Flip the board over and solder the components in place as shown in the pictures. Be sure the iron is fully warmed up before soldering. Do the pins on the IC as quickly as possible - ICs do not like high temperatures. Check for solder bridges and remove any that might have formed. The black wire on the board isn't needed, just solder the long black wire in where the lower end of the black wire is. (I thought I might need to put a resistor in where the short black wire is, but in the end it wasn't needed.) Sorry about the blurry image, here is what the back of the board will look like:
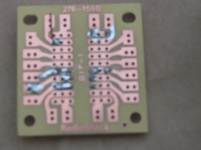
7. Cut 2 18" pieces of the green wire and 1 each 18" pieces of the red and black wire. Strip 1/4" from one end and a bit more from the other. Solder the 1/4" ends into the circuit board as shown in the diagrams and pictures.
8. Trim the excess wire and component leads on the metallic side. This is what the board will look like with the wires in place.
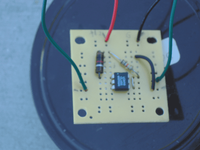
9. Test the circuit. Attach the Red wire to the positive terminal of the 9V battery, and the Black wire to the negative terminal. Set the multimeter to measure in the lowest DC voltage range greater than 9V. For most multimeters that is most likely 20VDC. [Some multimeters apparently have a "9V" setting - that is for testing batteries, not for measuring voltage. Do not use it.] Connect it between the negative terminal of the battery and the green wire attached to pin 6. It should read 9V (whatever the battery is reading.) Touch the Green wire attached to pin 2 of the IC to the negative terminal of the battery. The voltmeter should drop to very close to zero volts.
(continued in next post)
Last edited: